Introduction:
The Laogongyingzi Coal Mine coal preparation plant, located in Inner Mongolia, traditionally relied on a screening, picking, and crushing process system. The raw coal was classified into 80 (70) mm and 30 mm grades, with manual selection of large coal blocks. This method posed significant challenges, including high dust and noise levels, safety hazards, labor intensity, and low sorting efficiency. To address these issues, the mine has upgraded its system with an advanced dry coal sorting technology.
Project Overview:
– Location: Inner Mongolia
– Production Capacity: 1.80 Mt/a
– Challenges: High dust and noise, safety hazards, intensive labor, and low sorting efficiency
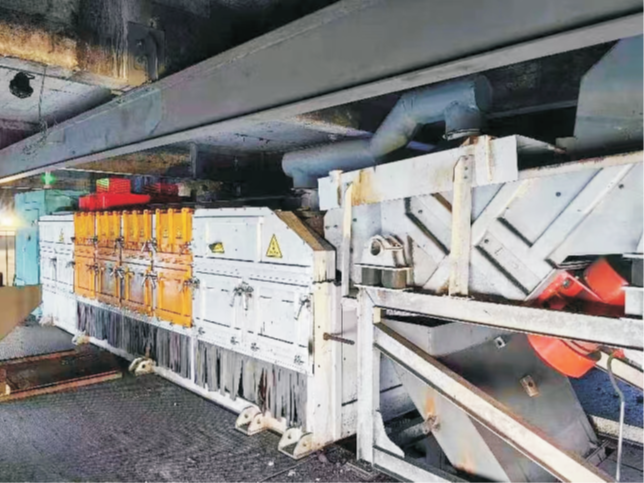
Solution:
Advanced Dry Coal Sorting System:
To improve working conditions, enhance safety, reduce labor intensity, and boost sorting efficiency, Laogongyingzi Coal Mine introduced a dry coal sorting system. This system sorts raw coal blocks of -80 (70) mm and above, effectively separating clean coal blocks from Reject blocks.
– Processing Particle Size: Pre-reject Reject from +70-400mm raw coal
– Machine Used: 1 FHG-1600-X Golden Coal Series dry coal sorting machine
– Single Machine’s Processing Capacity: >180 t/h
Key Features:
– Intelligent Sorting: The system can perform intelligent coal-reject sorting while retaining manual selection functionality in case of system failure.
– Manual Selection Channel:
- A manual selection channel is reserved at a suitable position to ensure continued operation during machine downtime.
- By adjusting the speed of the raw coal belt inside the sorting machine to 0.5m/s, manual picking can be carried out efficiently.
– Improved Working Conditions: Reduces high dust and noise levels, ensuring a safer and more comfortable working environment.
– Increased Efficiency: Provides a workstation for four people to simultaneously pick up Reject, enhancing labor efficiency and safety.
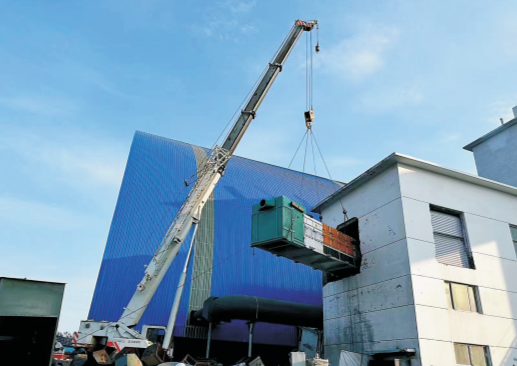
Sorting Results:
– Coal in Reject: <1%
– Reject Discharge Rate: >95%
Benefits and Outcomes:
– Enhanced Safety and Working Conditions: Significantly reduces dust and noise, minimizing safety hazards and improving the overall work environment.
– Higher Sorting Efficiency: Achieves a Reject discharge rate of over 95% with less than 1% coal in the Reject.
– Flexibility: Maintains the ability for manual selection to ensure uninterrupted operation during system failures.
Conclusion:
The upgrade to an advanced dry coal sorting system at Laogongyingzi Coal Mine has transformed the coal preparation process, enhancing safety, efficiency, and productivity. This innovative solution demonstrates the effectiveness of integrating intelligent sorting technology to address traditional coal preparation challenges.